Before My Toolmania WBM16LV milling machine was delivered I already had plans to convert it to a CNC milling machine.
I do have some experience with 3d printing, and I have 2 CNC routers up and running, like the Indymill. So, the conversion of this mill will not be difficult in the Technical sense. But- making the perfect designs for the adapter plates of the Y- and X- axes proved to be a lot more work than I expected.
The column cutter is already equipped with glass scales with digital readout. Furthermore, there is a gas spring mounted on the Z-column so that not all the weight is in the way when moving back and forth. Also an automatic lubrication system for the slides of X, Y and Z-axis will be mounted.)
DOWNLOAD ALL MY CNC TEETHED ADAPTER DESIGNS as .STL files
The electronics will become OpenCNC + wifi + wireless controlbox. I received the kit and will put it together the coming weeks. For now I am going to set the mill up with my all-in one USB-CNC-MDK2 board. I use this for all of my routers and mills to get it set up in first instance since it is very simple and sturdy. And- you can run it instantaniously without any PC or programming, just with the handwheel or from SD card. And from the laptop, of course.
DOWNLOAD MY CNC ADAPTER DESIGNS as .STL files
LATEST NEWS:
After this all worked well, I also made designs for NEMA direct drive adapters on my Toolmania MiniMill:

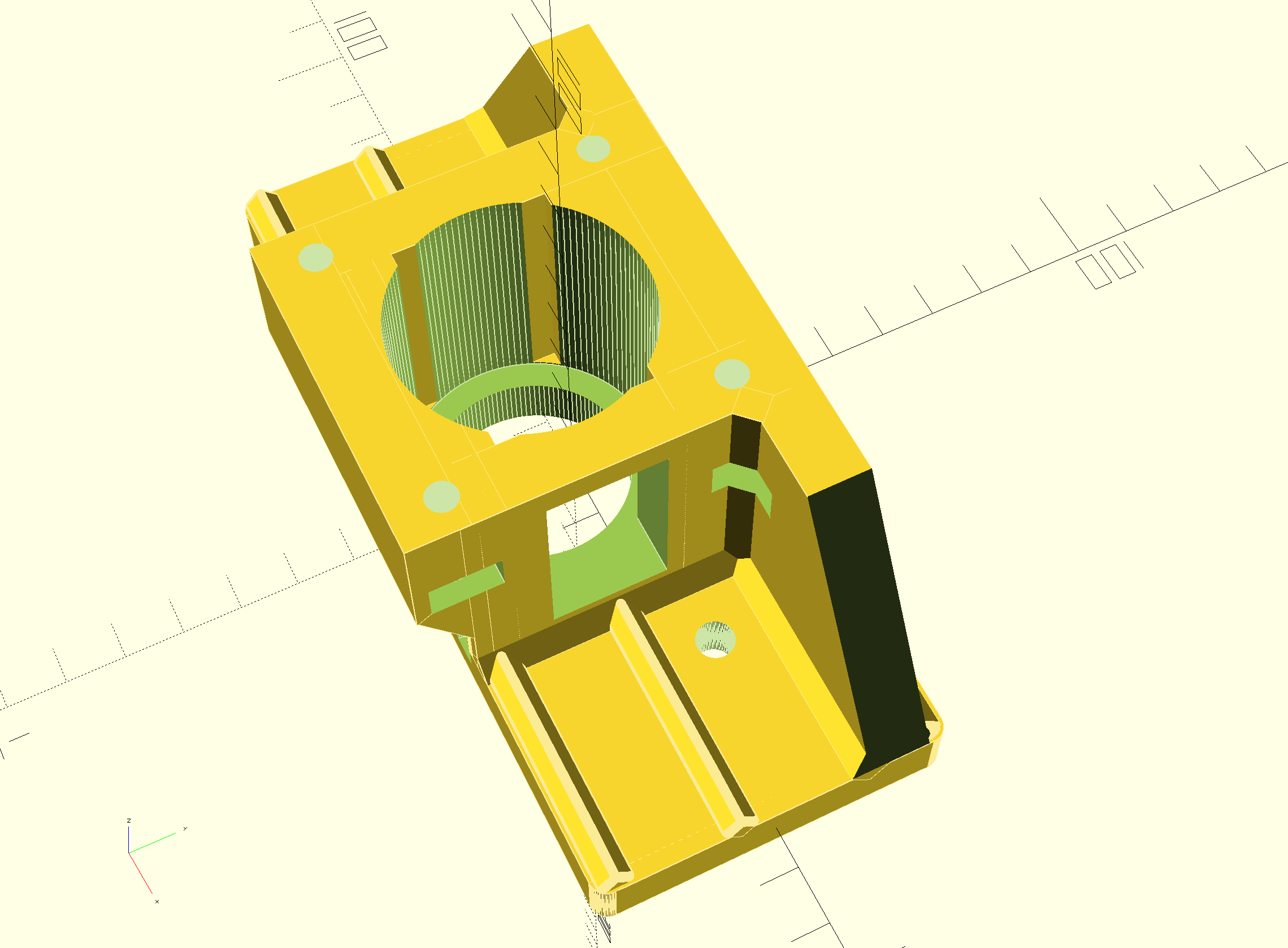
Above: Direct drive adapter for the Z-axis
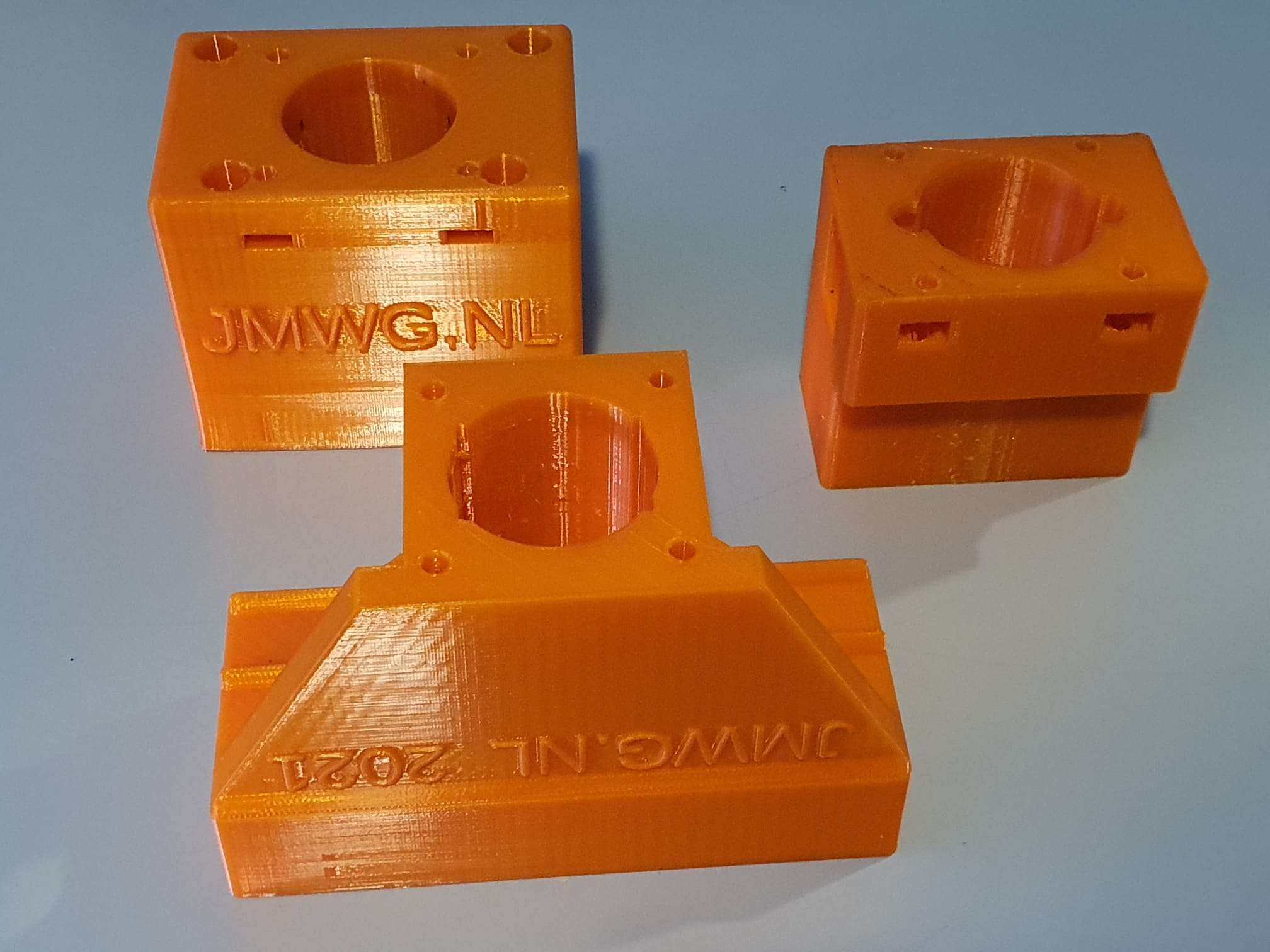
What makes it tricky is the choice to make: Will I replace the spindles with ball bearing spindles or not? Not for the time being, first let’s make everything on CNC and then I’ll see how it goes.